- Surface Finishing Service
Surface Finishing
Surface Finishing, also called metal surface treatment, is a process for artificially forming a surface layer different from the mechanical, physical and chemical properties of the substrate on the surface of the substrate, in order to meet the corrosion resistance, wear resistance, decoration or other special functional requirements of the product. Zehan Provides a variety of subsequent surface treatments that meet the performance requirements of the product.
Gold Plating
The use of electrolysis or other chemical methods to attach gold to the surface of metal or other objects to form a thin layer of gold.
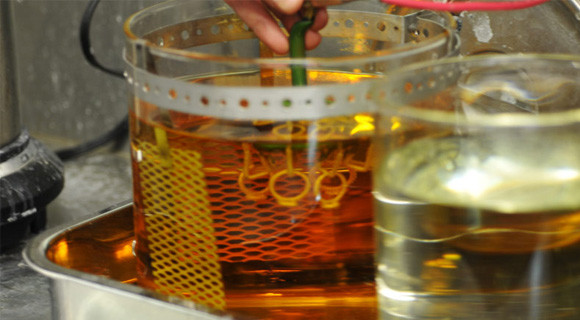
Silver Plating
The coating is used to prevent corrosion and increase conductivity, reflectivity and aesthetics. Widely used in the manufacturing industries such as electrical appliances, instruments, instruments and lighting appliances. The silver plating layer is much cheaper than gold plating, and has high conductivity, light reflectivity and chemical stability to organic acids and alkalis. Much more than gold
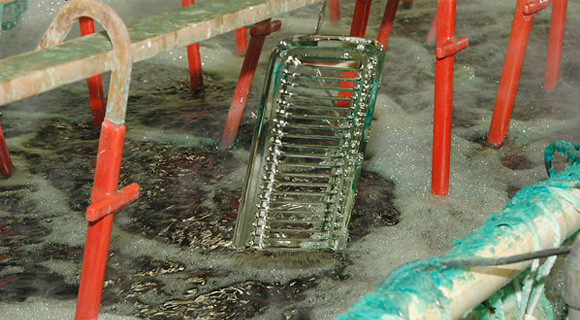
Zinc Plating
Zinc plating refers to the surface treatment technology of plating a layer of zinc on the surface of metal, alloy or other materials for aesthetics and rust prevention. It is mainly used to prevent corrosion of steel, its protective performance and coating thickness. The relationship is very big. After passivation , dyeing or coating of the photoresist, the zinc coating can significantly improve its protection and decorative properties.
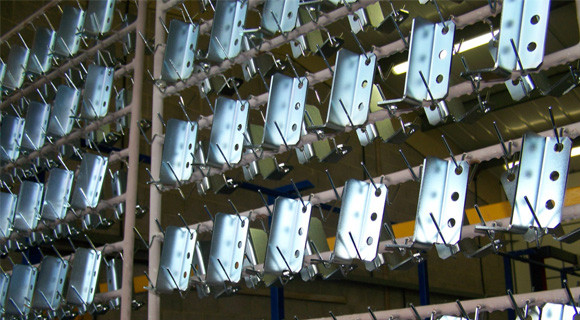
Hot-dip Galvanizing
Hot-dip galvanizing is a process technique in which a metal such as steel, stainless steel or cast iron is immersed in a molten liquid metal or alloy to obtain a coating. Hot-dip galvanizing is the most widely used and cost-effective steel surface treatment method in the world. Hot-dip galvanizing products play an inestimable and irreplaceable role in steel corrosion reduction, life extension and energy saving.
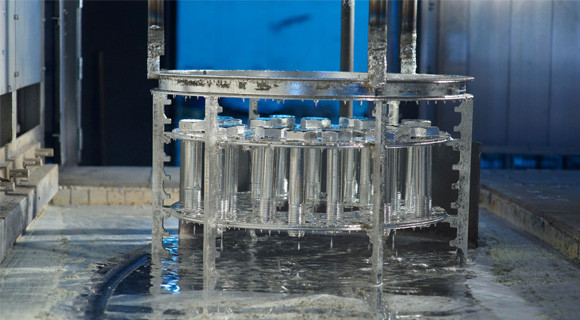
Chrome Plating
Chrome layer has high hardness, good heat resistance and gloss. The chrome layer has a low coefficient of friction, especially the dry friction coefficient, which is the lowest of all metals. Therefore, the chrome plating layer has good wear resistance.
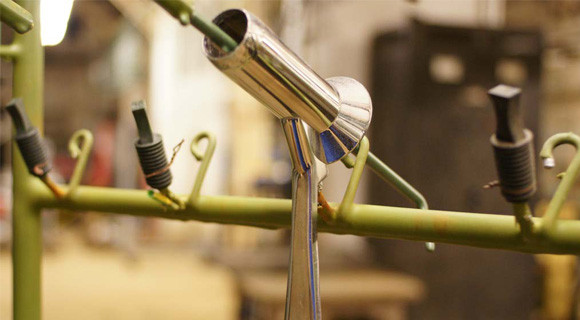
Nickel Plating
The electroplated nickel layer is highly stable in air and resistant to atmospheric, alkali and certain acid corrosion. The crystals are extremely fine and have excellent polishing properties. The polished nickel coating gives a mirror-like finish and maintains its luster for a long time in the atmosphere.
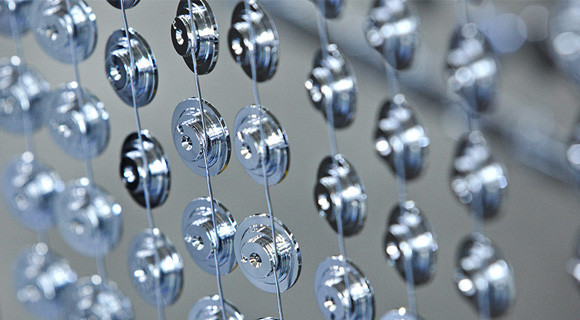
Anodizing
The process of forming an oxide film on an aluminum article (anode) of aluminum and its alloy under the corresponding electrolyte and specific process conditions due to the application of current. In order to overcome the defects of surface hardness and wear resistance of aluminum alloy, expand the application range and prolong the service life, surface treatment technology has become an indispensable part of the use of aluminum alloy.
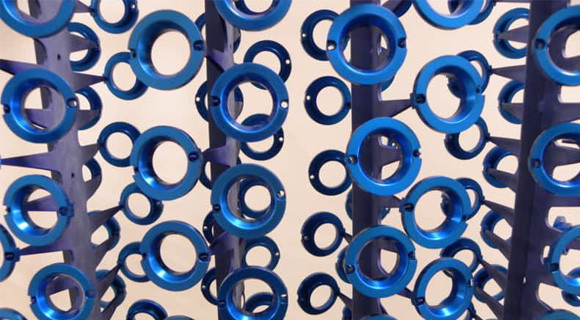
Black Oxide Coating
Black oxide coating is a common method of chemical surface treatment. The principle is to create an oxide film on the metal surface to isolate the air and achieve rust prevention. The surface of the steel parts is blackened, and it is also called blue.
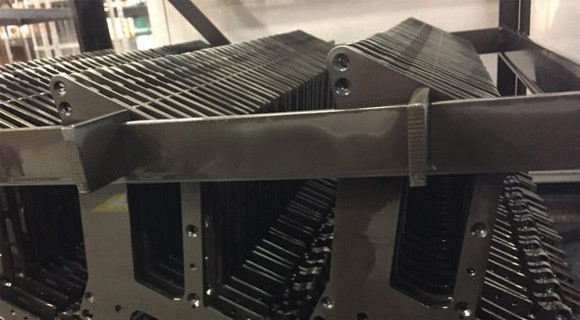
Powder Coating
It is a spraying technique in which the compressed air arch powder is dispersed into a powder mist particle under the action of high-voltage static electricity and adsorbed on the surface of the object by an electric field.
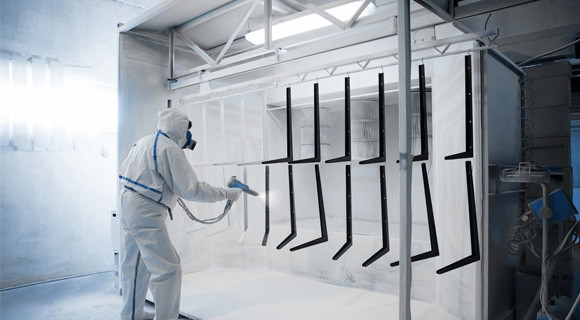
Spray Paint
Metallic surface painting is a method of protecting metals from oxidative corrosion. Spray painting on metal surfaces is an important means of metal corrosion protection. The good paint coating protection layer is continuous and intact, and the combination is good, which can become a barrier to inhibit the intrusion of corrosive media.
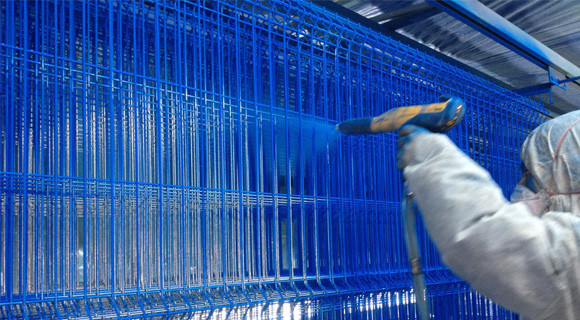
E-coating
E-coating is obtained by immersing the conductive object in a relatively low concentration e-coating tank filled with water as an anode (or cathode), and further providing a corresponding cathode (or anode) in the tank, indirectly at the two poles. After a period of DC current, a special coating method is formed on the surface of the object to be coated, which is uniform and fine, and is not dissolved by water.
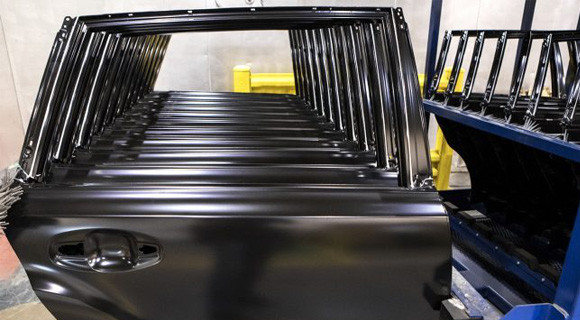
Dip Molding
The metal product is used as a core, impregnated with pvc emulsion paste, and the coated product obtained by plasticizing and cooling is called PVC plastic product. Because of its beautiful appearance and good hand feeling, it is coated with pliers. Casting products such as dumbbells.
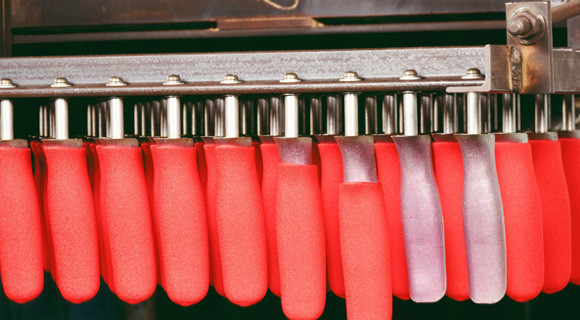
What Industries Use Metal Surface Treatment ?
Almost every industry will have a need for metal surface treatment equipment. Among the industries who today use metal surface treatment include the following; the automotive industry, the construction industry, the Container industry, the electrical industry, the medical industry, industrial equipment, industries using laboratory equipment, aerospace, and several
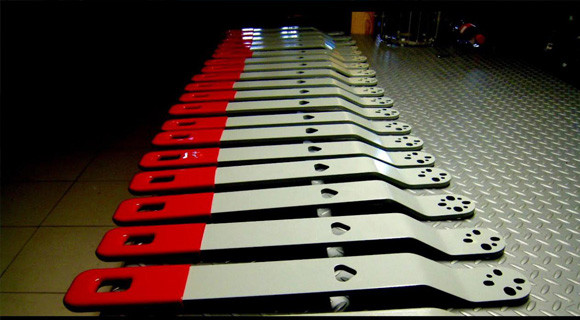